We have stumbled upon two talented craftsmen who caught our attention. Jasper Overgaard and Christian Dyrman started the company Overgaard & Dyrman. Together they make the marvellous furniture seen on the pictures; their design and production.
How did you find each other?
First time we met was at the engineering studies at Aalborg University in 2005, where we were both accepted at the course of Architecture and Design. We both decided to embark on this education due to the connection between architecture and design. An approach with competencies within both a creative and a technical field seemed very attractive to us and is something we use a lot today.
What inspired you to make furniture?
We realised very early that we both had a good understanding for the creative process. At the study of engineering we managed to make a lot of projects together. We even wrote a report of 100 pages for one of them; it was meant to contain a lot of text and graphic material to support the work of a building or a product. Our problem was that even though we were good at drawing in 3D and making complex calculations, it never let to the making of an actual physical product. We missed the hands on part that the university did not prioritise.
Half way through our studies we got the opportunity to make a piece of furniture. We then decided to do something about it and found some local suppliers, who could help us with materials and know-how. We made a piece of furniture that was a bit more detailed and complex that the teachers were used to see. We were fascinated by the idea of making furniture.
This lead to that we both applied for the Royal Danish Academy of Fine Arts Schools of Architecture, Design and Conservation. We both did our masters in Furniture & Spatial Design. In contrast to the other students we would spend our time in the workshops that were available for us to use. We were very happy for this and it was far from what we used to in Aalborg.
I believe that over time the chair is one of the most frequent designed products and I do not think it is by coincidence. Even though there has also been made a lot of insignificant chairs, there are many interesting aspects in the making of a chair – or another furniture for that matter; aspects such as durability, ergonomic/comfort, materials, a smart structural construction and not least proportions and an interesting visual appearance.
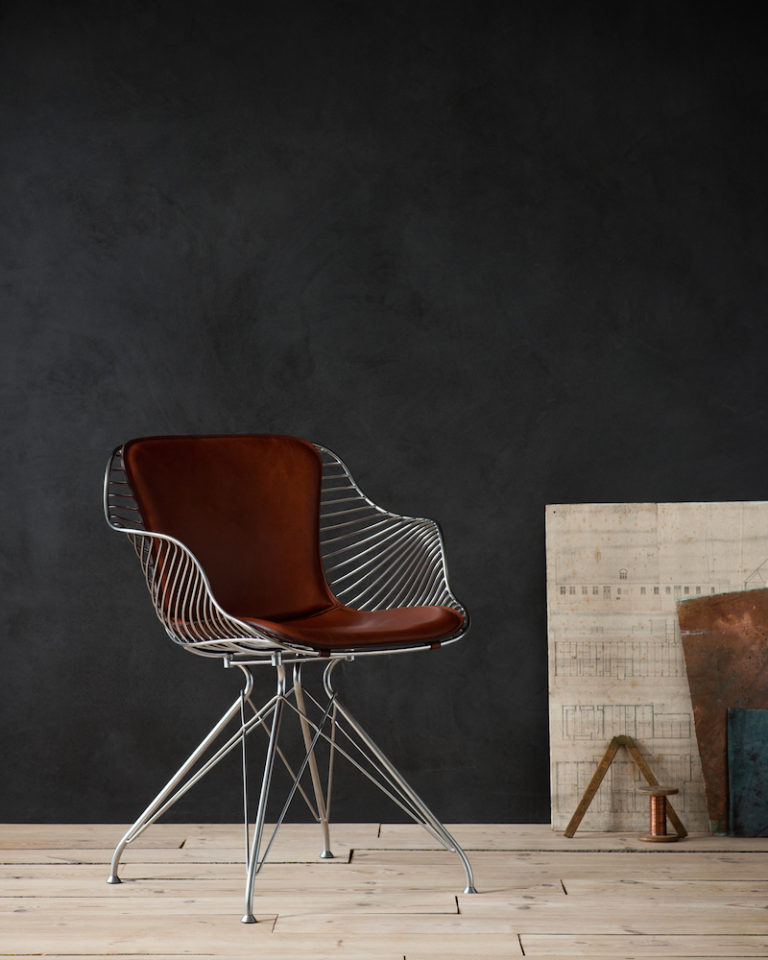
How long is the process of making one wire chair?
There are a lot of links of a production that takes many work hours. At times we hear that people get shocked by that we will allow ourselves to spend that many hours on a piece of furniture. This also results in the fact that our furniture gets relatively expensive at the end. The other day someone told us that it is ridiculous that we weld by hand instead of using robots. To that we can only reply that our method is the only way we make the product we wish without compromising the design and quality. Of course welding with a robot is an option, but that also means you have to adapt your furniture to that; to work from the point of technology and not your wishes of design and quality. If you try to make your product fit a certain technology the product will often end up a little dull. We would much rather create products that reflect passion and concentration by the craftsman rather than products that are spit out in thousands.
How would you describe your personal design style?
Our style is both classic and modern and with a twist from the old times, when there was respect for craftsmanship and the sense of detail.
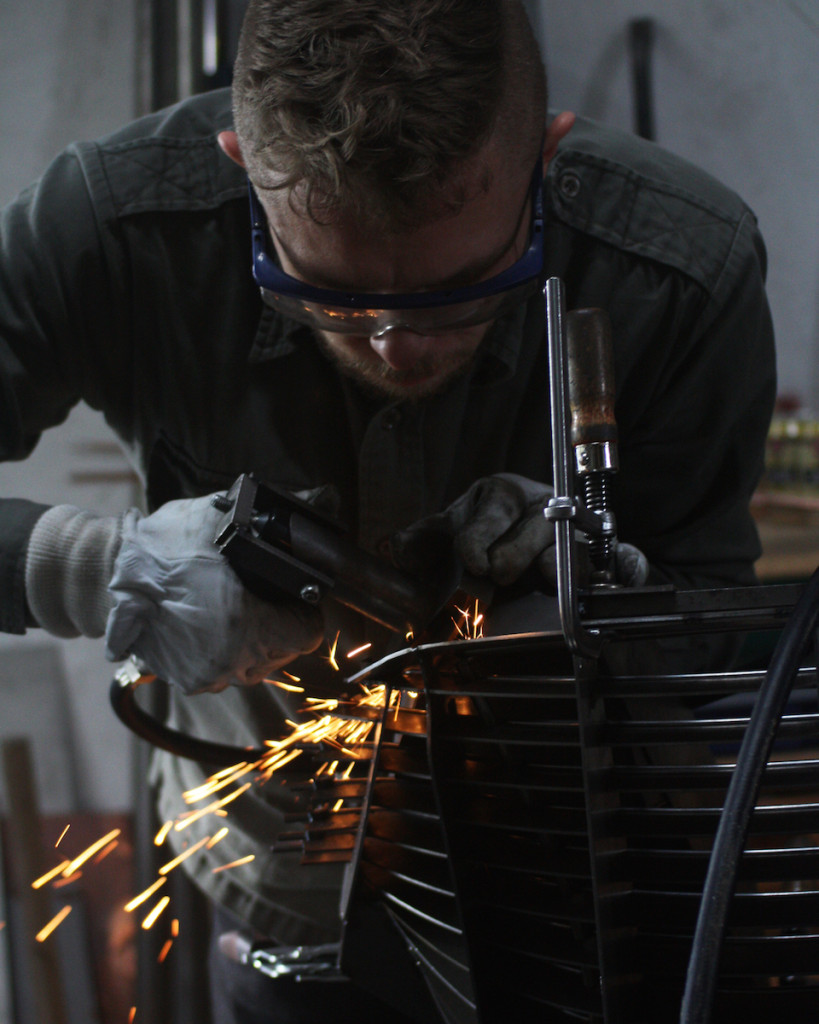
What is your biggest achievement so far?
I believe we both expect the biggest achievement to be just around the corner. We enjoy challenging ourselves and hopefully we are able to keep on taking the company and our approach of design to new heights.
But to answer your question, our biggest achievement must be that we have been able to design, develop and setup a production of a rather complex furniture collection. In that process we have had many small victories.
I would say that it is when we have been talking to craftsmen of metal and saddle making, that we have received the most acknowledgements. It always weighs a little more when it comes from people who know what they are talking about.
What are your dreams of Overgaard & Dyrman?
We hope that Overgaard & Dyrman can develop dynamically, so that we can build a fantastic company with enthusiastic employees, who share our passion of making design without compromises. This may be in making furniture, but we also hope to make other projects in the long run. This could be a complete project within interior architecture or a product in collaboration with a company that makes something entirely different, but shares our approach to design.